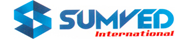
We offer heatless compressed air dryer which are the simplest form of desiccant type gas or air dryer (drier). Our products range is perfect for achieving a dew point of -400C for compressed air dryer systems and other gas and air dryer (drier) applications.
Extensive Mimic display with Electronic Controller
Energy saving purge economiser
Stainless Steel Filters Catridges
Fabrication Code : IS 2825
Dewpoint better than -40º C
Fabrication Code : ASME SEC VIII DIV I
Dewpoint based changeover
Highlight :
Purge Economiser :
By setting a switch in the controller at a percentage of maximum flow, the controller will close the purge valve when sufficient purge air has been used. This reduces purge loss according to air usage. The purge loss, which is 14% normally reduces to as low as 5.6%.
Requirement : | |||||
Flow Volume : | 175 cfm | ||||
Working Pressure : | 6 Kg / cm2 | ||||
Inlet air Temperature : | 450c | ||||
Referring the Graphs : | Factor (T) = 0.9 Factor (P) = 0.88 | ||||
Dryer capacity required : |
|
= 220.9 cfm |
Model | Inlet Flow cfm | End Connection | Dimensions (mm) | Weight Kg | ||
Height | Width | Depth | ||||
DP - 192 | 114 | 1" BSP | 2000 | 750 | 650 | 380 |
DP -288 | 172 | 1" BSP | 2050 | 750 | 650 | 440 |
DP - 384 | 229 | 1 1/2" BSP | 2100 | 750 | 650 | 550 |
DP - 480 | 286 | 2" NB | 1670 | 1100 | 1300 | 620 |
DP - 576 | 343 | 2" NB | 1880 | 1100 | 1300 | 700 |
DP - 768 | 458 | 2"NB | 1810 | 1200 | 1300 | 850 |
DP -960 | 572 | 2"NB | 1830 | 1300 | 1300 | 950 |
DP -1440 | 860 | 3"NB | 1975 | 1500 | 1500 | 1265 |
DP - 1920 | 1144 | 3"NB | 2100 | 1500 | 1500 | 1575 |
Operating voltage - 230 V AC 50 Hz 1 Ph.
For any other capacity contact factory.
Specifications are subject to change without notification.
Pre-filteration :
The moisture laden compressed air passes through the pre filter, here moisture load is reduced through coalescence. Condensation is removed through the drain valve ADV1. At the oil filter oil vapours are removed completely, small level of water condensation is purged through the valve ADV2.
(Please refer figure) The Towers are filled with Activated Alumina as desiccant (Molecular sieve available as option). When air passes through Tower 1 which consists of ”DRY” Desiccant, it gets completely dried, and passes through check valve and after filter. At the after filter, Desiccant fines are removed. Therefore dry compressed air passes out at the outlet.
(Please refer figure) Regeneration takes place in 2 stages a) De-pressurisation b) By passing Dry air. Tower II consists of fully moist desiccant at pressure. This is suddenly De-pressurised by opening the purge valve. Water molecules seep out of the desiccant and appear on the surface. “Super Dry” purge air passes through the Regeneration “Nozzle” and the desiccant bed thereby completely carrying away the water molecules. Tower II gets regenerated and is ready for the next drying cycle after the re-pressurisation.